Top 25 Essential Boiler Interview Questions Every Fresh Marine Engineer Should Know
- Team Dmet Club
- Jul 18, 2024
- 7 min read
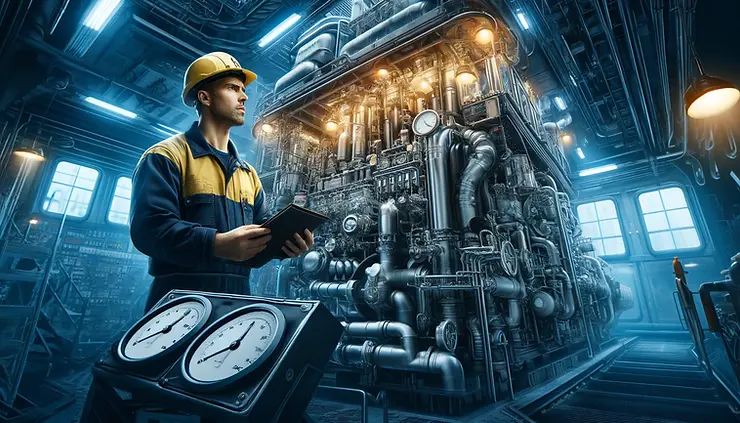
Entering the world of marine engineering as a fresh graduate is both exhilarating and challenging. Among the various systems and components you'll encounter, the boiler stands out as one of the most critical.
Mastering the fundamentals of boiler operation, maintenance, and troubleshooting is essential for any aspiring marine engineer. Whether you're preparing for your first job interview or aiming to enhance your understanding of this vital machinery, having a solid grasp of boiler-related knowledge can set you apart from the competition.
In this blog, we’ve compiled the top 25 essential boiler interview questions that every fresh marine engineer should know. These questions cover a wide range of topics, from basic definitions to intricate operational details, and are designed to help you demonstrate your technical expertise and readiness to tackle real-world challenges.
By familiarising yourself with these questions, you'll not only boost your confidence but also showcase your preparedness to potential employers, making a strong impression during your interviews. Dive in and get ready to ace your boiler interview questions with confidence and clarity!
Question 1: What is a boiler?
A boiler is a critical component in marine engineering, responsible for generating steam by heating water. It is a closed vessel where water is heated and converted into steam under pressure. The produced steam is utilized for various purposes, including propulsion, heating, and powering auxiliary machinery onboard ships.
Question 2: What are the uses of steam onboard?
Propulsion: Powers steam turbines or engines.
Electricity: Generates power through steam turbines.
Heating: Warms accommodation, cargo, and tanks.
Hot Water: Supplies hot water for showers and kitchens.
Desalination: Converts seawater to fresh water.
Cargo Operations: Heats tanks for easier cargo transfer.
Sterilization: Cleans medical and food preparation areas.
Air Conditioning: Supports cooling systems indirectly.
Turbine Maintenance: Cleans turbine blades.
Firefighting: Assists in firefighting operations.
Question 3: Name Boiler mountings and alarms.
Boiler Mountings:
Safety valve
Water level indicator
Pressure gauge
Steam stop valve
Blowdown valve
Boiler Alarms and Trips:
Low water level alarm
Low-low water level alarm
High water level alarm
High-high water level alarm
Low steam pressure alarm
High steam pressure alarm
Low feed-water pressure alarm
Low fuel oil pressure alarm
Low fuel oil temperature alarm
High fuel oil temperature alarm
Low combustion air pressure alarm
Low atomising steam pressure alarm
Flame failure alarm
Burner not in firing position alarm
Question 4: What are the different types of boilers?
Fire Tube Boilers: Water surrounds the tubes through which hot combustion gases pass, typically used for low to medium steam pressures.
Water Tube Boilers: Water flows through tubes surrounded by hot combustion gases, used for high-pressure applications and generating large amounts of steam.
Package Boilers: Compact boilers that come pre-packaged with all necessary components for easy installation and use.
Question 5: Difference between fire tube and water tube boiler?
Fire Tube Boiler:
Structure: Water-filled tubes surrounded by hot gases.
Pressure: Low to medium.
Steam Capacity: Lower, up to 20,000 kg/hr.
Size: Compact.
Usage: Small to medium applications.
Efficiency: Less efficient.
Maintenance: Easier.
Applications: Heating, small-scale industrial processes.
Examples: Cochran boiler, Scotch marine boiler.
Water Tube Boiler:
Structure: Water flows inside tubes, surrounded by hot gases.
Pressure: Medium to high.
Steam Capacity: Higher, more than 20,000 kg/hr.
Size: Larger and heavier.
Usage: High-pressure applications, power generation.
Efficiency: More efficient due to larger heating surface.
Maintenance: More complex.
Applications: Power plants, large industrial processes.
Examples: Babcock and Wilcox boiler, Stirling boiler.
Question 6: Tell me about gauge glass blown down?

Question 7: Describe boiler water test
Boiler water testing is crucial for maintaining water quality and preventing issues like scaling and corrosion. Common tests include:
Alkalinity Test: Measures alkaline compounds to prevent corrosion and scaling.
pH Test: Ensures water pH is within the safe range (typically 9-11).
Hardness Test: Detects calcium and magnesium ions that cause scale.
Chloride Test: Monitors chloride levels to prevent corrosion from seawater ingress.
Conductivity Test: Measures total dissolved solids (TDS), indicating water purity.
Phosphate Test: Checks phosphate levels used to prevent scale formation.
Dissolved Oxygen Test: Ensures low oxygen levels to prevent corrosion.
Question 8: What is the Temperature of an Exhaust gas boiler?
The temperature of an exhaust gas boiler (EGB) depends on various factors, including the type of fuel used, the load on the main engine, and the boiler design. Typical exhaust gas temperatures can range as follows:
At Full Load: 250°C to 400°C (482°F to 752°F).
After Heat Recovery: 120°C to 180°C (248°F to 356°F), depending on heat recovery efficiency.
Question 9: What is the pH value of boiler water?
The pH value of boiler water is crucial for maintaining efficiency and preventing corrosion and scaling. Typical pH ranges are:
Low-Pressure Boilers: pH 10.5 to 11.5.
High-Pressure Boilers: pH 9.0 to 11.0.
Question 10: What will happen if the pH value decreases in boiler feed water?
If the pH value of boiler feed water decreases:
Corrosion: Acidic water increases corrosion of boiler components.
Scale Formation: Lower pH can cause mineral deposits.
Reduced Efficiency: Corrosion and scale decrease operational efficiency.
Higher Maintenance Costs: More frequent repairs and maintenance are needed.
Leaks and Failures: Prolonged exposure to acidic conditions can result in hazardous leaks and system failures.
Question 11: What happens to the boiler if water contains chloride?
Chloride in boiler water can cause:
Corrosion: Accelerates metal corrosion.
Cracking: Can induce stress corrosion cracking.
Scale Formation: Contributes to scale buildup.
Foaming and Carryover: Increases risk of foaming and water carryover into steam.
Operational Issues: Requires frequent monitoring and treatment.
Question 12: Why do we carry out boiler water and cooling water tests?
Boiler water and cooling water tests are essential for maintaining the reliability, efficiency, and safety of industrial processes. Regular testing and appropriate water treatment help mitigate risks and extend equipment lifespan.
Question 13: How do we maintain low dissolved oxygen content in boiler water?
To maintain low dissolved oxygen content in boiler water:
Mechanical Deaeration: Use deaerators or oxygen scavengers.
Chemical Treatment: Add chemical oxygen scavengers like sulfite or hydrazine.
Feed water Quality: Maintain high standards to
dissolved oxygen ingress.
Temperature Control: Keep boiler water temperatures high to reduce oxygen solubility.
Continuous Monitoring: Regularly monitor dissolved oxygen levels.
Proper Venting: Ensure proper venting of air and gases.
Question 14: What is the working principle of flame eye?
The flame eye, or flame detector, works by sensing either infrared (IR) or ultraviolet (UV) radiation emitted by flames:
Infrared Detection: Detects heat radiation emitted by flames.
Ultraviolet Detection: Detects ultraviolet light emitted by flames.
Question 15: If the flame eye fails to detect the combustion, what will happen?
If a flame eye fails to detect combustion:
Fire Risk: Increased risk of fire or explosion.
Equipment Damage: Potential damage and operational downtime.
Safety Protocols: May fail to activate, leading to safety hazards.
Question 16: How do you test the flame eye?
To test the flame eye:
Inspect for damage or dirt.
Ensure correct power supply.
Use the test button, if available.
Simulate with UV or IR light.
Check indicator lights.
Adjust sensitivity.
Document results.
Follow regular maintenance guidelines.
Question 17: What are the mountings on the boiler?
The mountings on a boiler include:
Safety Valve
Water Level Indicator
Pressure Gauge
Steam Stop Valve
Feed Check Valve
Blow-off Cock
Fusible Plug
Manholes and Handholes
Question 18: What is a safety valve?
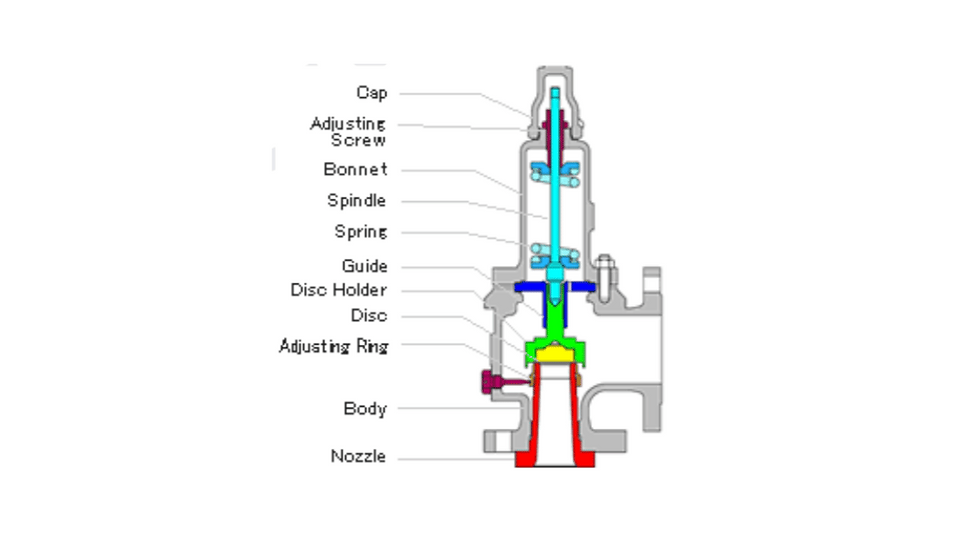
A safety valve is a crucial component used in boilers and pressure vessels to prevent excessive pressure buildup. It automatically releases steam or fluid when the pressure exceeds a preset limit, protecting the boiler from potential explosions or damage.
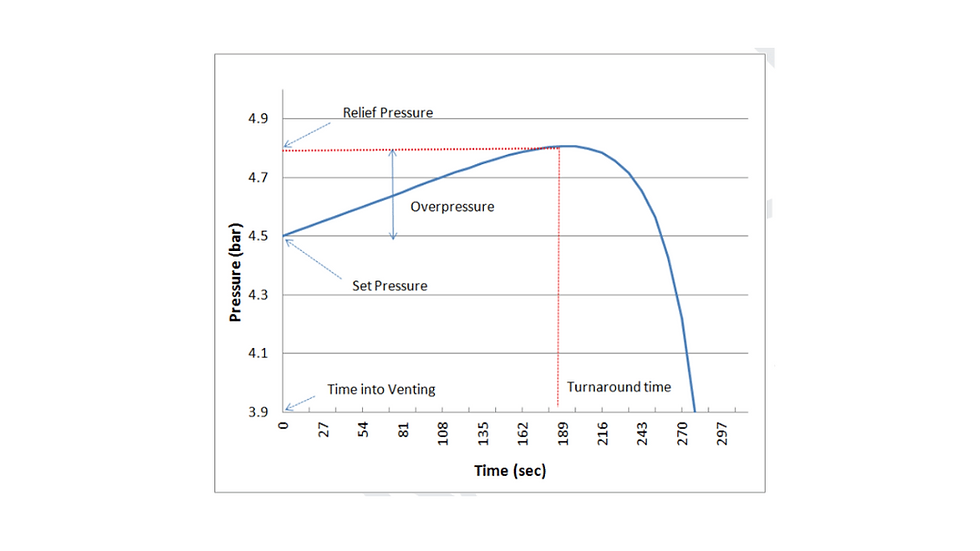
Question 19: What is a relief valve?
A relief valve is a pressure relief device that automatically releases excess pressure from a system. It opens when the pressure exceeds a predetermined set point, allowing the fluid to escape until the pressure drops to a safe level.
Question 20: What is the difference between superheated steam and saturated steam?
Question 21: What are the uses of superheated steam except turbine rotation?
Superheated steam is used for:
Heating: Preheating fuel oil before engine entry.
Drying: Drying cargo holds or cargo like grains.
Sterilization: Sterilizing equipment and spaces.
Power Generation: Driving auxiliary machinery.
Deaeration: Removing dissolved gases from feedwater.
Chemical Processes: High-temperature chemical processes.
Tank Heating: Heating tanks for various purposes.
Question 22: How can you remove water if it is present in steam?
To remove water from steam:
Use steam separators.
Ensure proper steam draining systems.
Install steam traps.
Use drip legs at low points in steam lines.
Consider steam dryers or superheaters.
Question 23: What are the effects of the presence of water in steam?
The presence of water in steam can cause:
Corrosion: Increased acidity leads to corrosion.
Reduced Efficiency: Lower heat content reduces efficiency.
Erosion: Water droplets erode turbine blades.
Loss of Performance: Incomplete combustion and reduced efficiency.
Scale Formation: Water impurities form scale.
Mechanical Damage: Water hammer causes mechanical damage.
Question 24: What is water hammering? What is the effect of water hammering?
Water hammering, or hydraulic shock, occurs when fluid rapidly changes direction or velocity within a piping system, creating a pressure surge.
Effects:
Mechanical Damage: Pipes, valves, and fittings can vibrate or rupture.
Noise: Loud banging or hammering noise.
Structural Fatigue: Leads to fatigue failure over time.
Reduced Lifespan: Accelerates wear and tear.
Safety Risks: Sudden failures or leaks pose hazards.
Question 25: What is the difference between an economizer and a boiler?
Question 26: Describe the functioning of water tube type boilers.
Water tube boilers use a network of tubes to circulate water, heated by a fuel source like gas or oil. As hot gases pass over these tubes, they transfer heat to the water inside, converting it to steam. The steam separates in a drum for various applications, while water returns for reheating. These boilers are efficient for generating high-pressure steam quickly, ideal for industries needing large steam outputs like power plants and refineries.
To present-day cadets,
You are not alone in this journey. We, the alumni of DMET, are with you, always!
Don't watch the clock; do what it does. Keep going!
These questions are curated through extensive research done by present cadets. A special mention goes to Cadet Kush Rana for coordinating with them.